Червячно-резьбошлифовальный станок КСМ HSS350
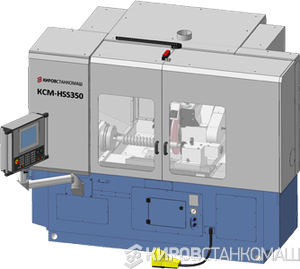
Червячно-резьбошлифовальный станок с ЧПУ SIEMENS 840Dsl создан на базе станка фирмы Klingelnberg модели HSS-350 и предназначен для обработки однониточным шлифовальным кругом одно- и многозаходных цилиндрических и глобоидных червяков с архимедовым, конволюнтным и эвольвентным профилем, а также резьбовых валов.
Благодаря двухкоординатному управляемому ЧПУ аппарату правки возможна шлифовка профиля
с различными модификациями.
После модернизации станку присваивается новое название модели - КСМ-HSS350.
Кинематика червячно-резьбошлифовального станка Klingelnberg HSS350 в ходе модернизации значительно упрощается за счет исключения сменных шестерен гитар настройки шага и деления, автоматической делительной муфты, что позволяет получить необходимую степень точности шлифуемых изделий.
Кинематическая схема до модернизации показана
на рисунке 2 а, после – 2 б.
Кликните на картинке, чтобы посмотреть ее в увеличенном виде |
|
![]() |
![]() |
Рисунок 2а Кинематическая схема станка до модернизации |
Рисунок 2б Кинематическая схема станка после модернизации |
Для управления всеми функциями станка используется система ЧПУ Sinumerik 840Dsl фирмы SIEMENS с оригинальным программным обеспечением.
Станок имеет 8 осей, из которых 7 управляемых (4 линейных и 3 круговых) и одна наладочная (ручная):
- Ось X – радиальная подача шлифовальной бабки (шлифовального круга);
- Ось Z – осевая подача стола (заготовки);
- Ось V – поперечная подача аппарата правки шлифовального круга;
- Ось W – продольная подача аппарата правки шлифовального круга;
- Ось А – поворот (наладочный) шлифовальной бабки (шлифовального круга);
- Ось B – вращение алмазного ролика аппарата правки;
- Ось C – круговая подача заготовки;
- Ось D – вращение шлифовального круга.
Рисунок 3. Компоновочная схема станка
С целью повышения степени точности шлифуемых изделий все линейные оси станка (X, Z, V, W) и ось круговой подачи (С) оснащаются высокоточными датчиками перемещений фирмы Heidenhain.
Скорость вращения шлифовального круга, параметры обрабатываемой заготовки и другие параметры устанавливаются вводом в программу с панели оператора или автоматически с выбором программы конкретной детали.
СИСТЕМА УПРАВЛЕНИЯ
- УЧПУ Sinumerik 840Dsl;
- Система цифровых преобразователей Sinamics S120;
- Синхронные бесщеточные двигатели перемещения по осям серии 1FT7 и 1FK7 с высокой точностью вращения (позиционирования);
- Асинхронный двигатель с короткозамкнутым ротором вращения шлифовального круга серии 1РН8
с бесступенчатой регулировкой скоростей; - Панель оператора SINUMERIK серии OP с цветным дисплеем TFT.
Рисунок 4 Компоненты системы управления
Применяемая электроавтоматика фирмы ABB, смонтирована в электрошкаф фирмы Rittal, производства Германии, оснащенный кондиционером.
Гидравлический насос фирмы «Marzocchi» и модульная гидроаппаратура «Duplomatic» производства Италия в составе гидростанции с контролем уровня масла, расположены в передней полости станины. Примененная система смазки состоит из импортных комплектующих «ILC» производства Италии и имеет электрический контроль и управление от системы ЧПУ станка.
Очистка СОЖ, поступающей из рабочей зоны, осуществляется с помощью центрифуги, смонтированной в баке емкостью 340 л. Для очистки рабочей зоны от отходов обработки, станок оснащен пистолетом для СОЖ. Туман из шлифовальной пыли и СОЖ удаляется из рабочей зоны с помощью системы фильтрации фирмы LOSMA, производства Италия.
Точная динамическая балансировка шлифовального круга осуществляется непосредственно на станке при помощи балансировочной системы фирмы Balance System, производства Италия.
Подготовка воздуха, необходимого для продувки оптических измерительных датчиков, осуществляется аппаратурой фирмы Heidenhain, производства Германии. Для очистки обработанных деталей от СОЖ, станок оснащен пневматическим пистолетом.
Аппарат правки с алмазным правящим роликом, специально разработан под задачу профилирования абразивных кругов применяемого типоразмера для создания необходимого профиля.
Рисунок 5 Аппарат правки
Размер рабочей зоны аппарата правки и форма рабочего профиля алмазного ролика (см. рисунок 6) позволяют обработать профиль круга с любой модификацией.
Рисунок 6 Рабочая зона аппарата правки
Для узлов аппарата правки выполнены проверочные расчеты на прочность и жесткость, в том числе с использованием метода конечных элементов (МКЭ), а также частотный анализ, позволяющий избежать нежелательных резонансных режимов работы.
![]() |
![]() |
Рисунок 7 Шпиндель аппарата правки с сеткой конечных элементов | Рисунок 8 Смещение переднего конца шпиндельного узла аппарата правки при максимальной нагрузке |
Наименование параметра | ЕИ | Значение | |
---|---|---|---|
Диаметр обрабатываемой детали | наименьший | мм | 10 |
наибольший | мм | 350 | |
Модуль обрабатываемого червяка | наименьший | мм | 0,5 |
наибольший | мм | 25 | |
Степень точности обрабатываемых червяков по ГОСТ 3675-81 | 5 | ||
Наибольший угол подъема винтовой линии | 45 | ||
Угол зацепления | наименьший | град. | 0 |
наибольший | град. | 30 | |
Шаг червяка | наименьший | мм | 1 |
наибольший | мм | 500 | |
Наибольшая длина шлифования | мм | 500 | |
Наибольшая глубина шлифования | мм | 65 | |
Расстояние между центрами | наименьший | мм | 100 |
наибольший | мм | 750 | |
Проходное отверстие шпинделя изделия | мм | 110 | |
Наибольшая частота вращения заготовки | мин-1 | 26 | |
Диаметр шлифовального круга | наименьший | мм | 300 |
наибольший | мм | 500 | |
Ширина шлифовального круга | мм | 16/25/40/63 | |
Наибольшая частота вращения шлифовального круга | мин. | 3000 | |
Осевая подача изделия | мм/мин. | до 3500 | |
Радиальная подача инструмента | мин. | до 500 | |
Продольная подача аппарата правки | мм/мин. | до 4000 | |
Поперечная подача аппарата правки | мм/мин. | до 4000 |
СТАНДАРТНЫЙ КОМПЛЕКТ ПОСТАВКИ
- Червячно-резьбошлифовальный станок Klingelnberg HSS350 с электрошкафом;
- Запасные части и расходные материалы для эксплуатации станка в течение 1 года;
- Комплект технической документации
ОПЦИОНАЛЬНО ПОСТАВЛЯЕТСЯ
- Круги шлифовальные;
- Алмазные ролики для профилирования круга шлифовального;
- Оснастка и приспособления под конкретную деталь;
- Написание управляющей программы и отработка технологии шлифования конкретной детали